‘Slim’ Welltec® Puncher 218 creates multiple perforations in high-strength alloy 28Cr tubing
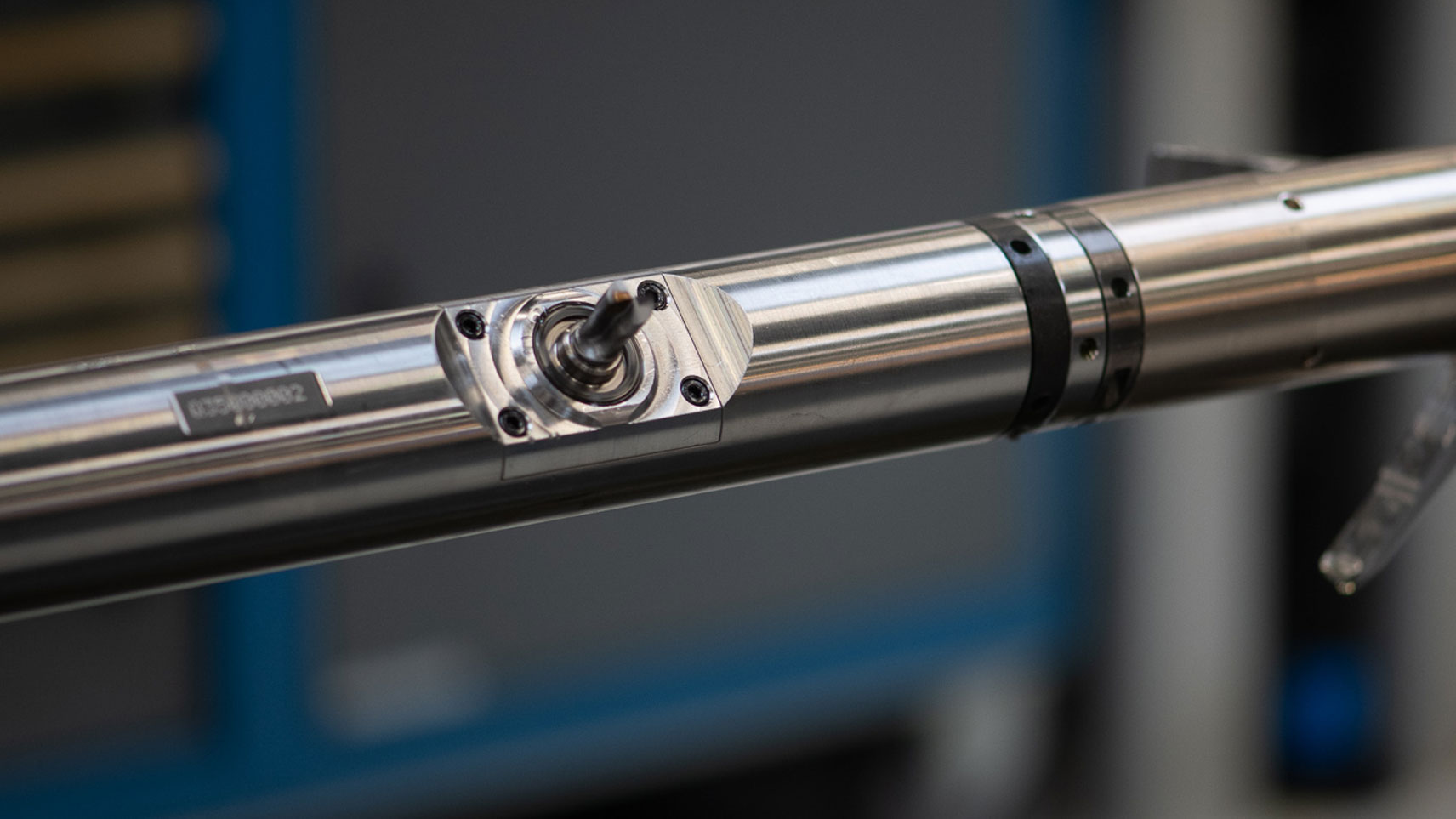
- Challenge: Plug and Abandonment
- Well type: Producer (shut-in)
- Formation temperature: 75°C / 167°F
- Well pressure: 3,000 psi
Background
During plug and abandonment (P&A) preparation offshore Denmark, TotalEnergies wanted to circulate trapped gas from a well by creating multiple perforations in the 4-1/2” tubing.
The chosen solution had to be capable of creating a predetermined number of uniform holes in the 28Cr alloy tubing, no doubt originally chosen for the completion due to its resistive qualities in a sour well environment with a high concentration of hydrogen sulfide (H2s). Furthermore, a subsequently planned tubing cut would also need to be carried out while the tubing was under compression.
Welltec deployed a mechanical tool suite including the ultra-slim Welltec Puncher 218 – a non-explosive method for equalizing pressures between tubular strings, utilizing a fast, surface-controlled drilling technique to produce precise, uniform holes with depth control to avoid damaging the casing behind.
Operation
Going into the operation, the plan was to create five, 12mm uniform perforations (holes) below the production packer.
The completion featured multiple jewelries and elements made out of Inconel, making the casing collar locator correlation rather challenging. Despite this, a good log reference was achieved with a sudden change in Casing Collar Locator (CCL) response, in-turn confirming the correct positioning above Wireline Re-Entry Guide (WREG).
The Welltec Puncher 218 was run in hole and positioned according to the CCL log and well schematics, creating all five perforations within a three-foot interval, on a single run. With surface readout (SRO) data providing good indications of success, the tool was pulled out of hole.
Although the client postponed the subsequent tubing cut for administrative reasons, the first planned phase was a complete success.
Achievements
The initial goal to mechanically punch five, 12mm holes in the 28Cr tubing was achieved quickly and efficiently, without damaging the casing behind (depth control), thus meeting the client’s primary objective to circulate out trapped gas.
The additional challenge of the highly resistant composition of the tubing did not prevent or affect the performance of the slim Welltec Puncher 218. A precise, safe, and non-explosive method for equalizing pressure(s) was provided, establishing the desired conditions for continuation of P&A operations.
Despite the postponement of the subsequent cut, Welltec provided a mechanical tool suite capable of a combined punch and cut single run, with the tubing under compression.